Introduction to PdM
Predictive maintenance (PdM) is a strategic approach used in modern industries to optimize productivity. It leverages IoT sensors and data analytics in real-time to monitor asset health and anticipate equipment failures before they escalate into significant disruptions.
However, Predictive maintenance goes way beyond these operational benefits for the pharma industry.
In addition to minimizing downtime and maximizing productivity, predictive maintenance enhances overall quality assurance efforts and mitigates non-compliance risk, giving producers high confidence in the products they deliver.
So, PdM is emerging as a strategic imperative for pharmaceutical companies seeking to uphold operational excellence and regulatory compliance.
The Evolution of Maintenance Strategies in Pharma
Historically, maintenance teams were like firefighters rushing to fix things once they were in flames. Their reactive approach meant waiting for the equipment to break down before taking action. But let’s face it: applying reactive maintenance in an industrial site means more downtime, less productivity, and a – huge – waste of money and resources.
Then, proactive strategies began to emerge. They were a step in the right direction but still had limitations. This approach meant implementing regular and scheduled maintenance to prevent breakdowns before they happen. However, it usually increased labor, parts, and downtime costs. Thanks to technological advancements, predictive maintenance technologies now enable maintenance teams to foresee equipment failures before they even occur. With real-time data, they can anticipate problems, saving time, money, and headaches!
So, it’s no wonder that more and more pharmaceutical companies are transitioning to a proactive maintenance mindset to optimize business performance and profitability.
Core Techniques of Predictive Maintenance
Predictive maintenance involves a collection of tools that vigilantly monitor the condition of the machinery, including:
Vibration Analysis
This technique focuses on detecting abnormal vibrations produced by machinery and equipment.
By understanding the nature of the vibrations, maintenance teams can identify patterns or anomalies indicating wear, misalignment, or other issues.
For instance, a tablet press machine in a pharmaceutical plant might show unusual vibrations. Their analysis could reveal early signs of bearing wear in the machine’s motor. The maintenance team could replace the bearings during a planned shutdown, preventing an unexpected breakdown and ensuring uninterrupted tablet production.
Thermography
Thermography is a non-invasive technique that uses infrared technology to detect and analyze temperature variations in machinery.
This solution enables technicians to identify overheating components, electrical faults, or abnormal temperature patterns
Let’s take the example of a clean-in-place (CIP) system that might show unusual temperature variations. Thermography would detect an overheating pump. The maintenance team could replace the faulty pump during scheduled maintenance, ensuring the continuous operation of the CIP system.
Ultrasound
This technology detects high-frequency sound waves from various sources, such as friction, electrical discharges, and fluid turbulence.
By detecting changes in ultrasonic patterns, maintenance technicians can identify potential issues such as bearing defects, leaks, and mechanical wear before they escalate into problems.
For instance, ultrasound technology could detect a small leak from an air compressor early on, allowing technicians to fix it during scheduled maintenance.
Oil Analysis
This PdM technique relies on regular examination of lubricating oils to gain insights into machinery health
This analysis reveals contaminants and indicators of wear or degradation, enabling early detection of abnormal conditions.
For example, oil analysis of a granulation machine might reveal metal particles in the lubricant, indicating early wear in the machine’s components. The maintenance team could then replace the worn parts during scheduled maintenance, preventing a breakdown and ensuring the machine continues to operate smoothly.
Motor Circuit Analysis (MCA)
MCA assesses the health of electric motors and their associated circuits. It involves analyzing various electrical parameters, such as voltage, current, resistance, and impedance, to detect abnormalities within the motor system.
Measurement and interpretation of these parameters allow technicians to diagnose issues like insulation loss, winding defects, or rotor bar problems.
For instance, MCA might reveal abnormal resistance in a mixing machine motor, indicating insulation loss. The operators could then repair the insulation on time, preventing motor failure and ensuring continuous operation of the mixing machine.
Benefits of Predictive Maintenance
Predictive maintenance provides many advantages that enhance the productivity and reliability of industrial pharmaceutical processes, some of these benefits being:
-
Increased asset uptime: Predictive maintenance keeps critical machinery operational for longer periods.
-
Lowered maintenance costs: Proactive interventions prevent costly breakdowns and emergency repairs, reducing maintenance expenses.
-
Greater energy efficiency: PdM helps identify and address inefficiencies in machinery operation to reduce energy consumption.
-
Optimized maintenance scheduling: Predictive solutions minimize downtime and increase productivity through efficient scheduling.
-
Increased production quality: Predictive maintenance ensures consistent production output by addressing potential issues before they escalate.
-
Enhanced worker safety and compliance: Avoiding failures helps to mitigate potential hazards, promote a safer working environment, and ensure regulatory compliance.
-
Extended equipment lifespan: Through regular monitoring and timely interventions, predictive maintenance extends the lifespan of machinery, maximizing its value.
Applications of Predictive Maintenance in Pharma
Predictive maintenance (PdM) is essential to pharmaceutical manufacturing process. By identifying and addressing potential equipment issues, PdM techniques minimize downtime and maximize production uptime. Moreover, it helps pharma companies to meet regulatory requirements by improving product performance and safety.
These benefits apply to the vast majority of assets directly or indirectly involved in the pharmaceutical production processes:
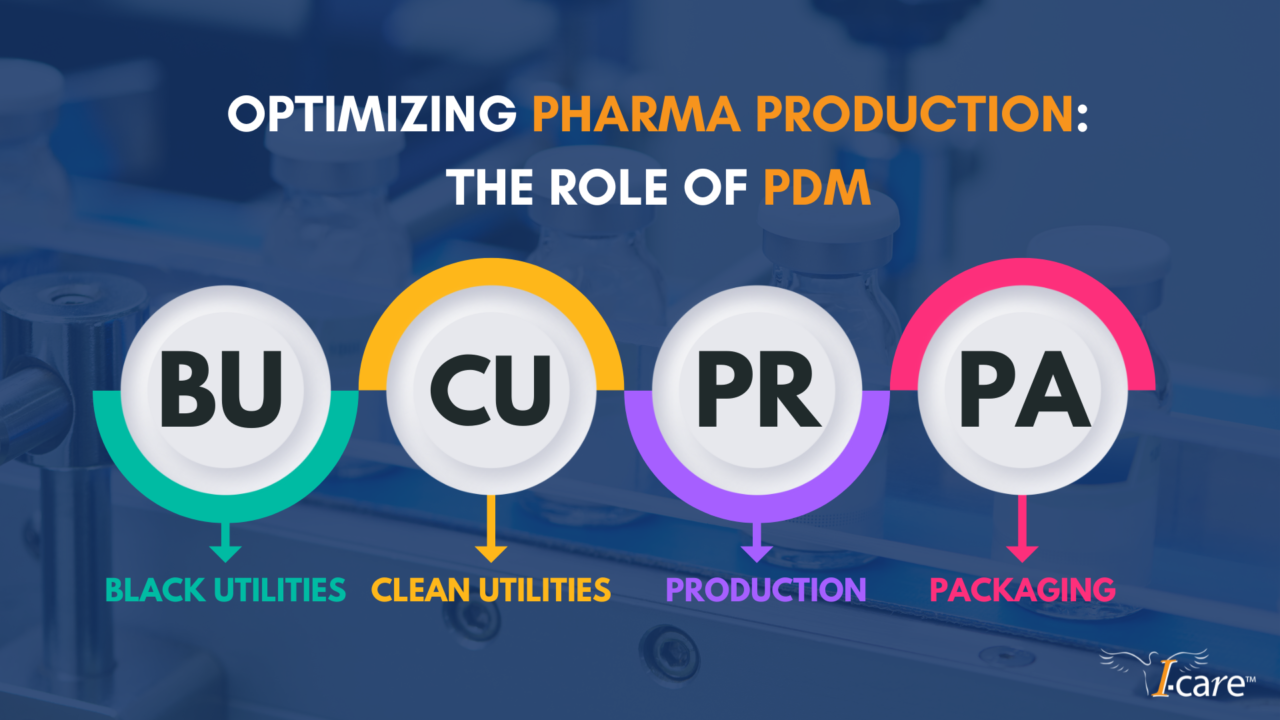
Black Utilities
These assets are not in direct contact with the pharmaceutical product but are crucial for manufacturing.
Black utilities typically include steam, chilled water, compressed air, and electricity. They are essential for providing energy, temperature control, and other support functions necessary for pharmaceutical production.
Implementing predictive maintenance for black utilities ensures they can continuously support the manufacturing processes and meet strict quality and regulatory standards.
Clean Utilities
Clean utilities are in direct contact with the pharmaceutical product during manufacturing and have the potential to impact its quality, purity, and safety.
These assets include purified water, clean steam, clean-in-place (CIP) systems, and sterile air. These utilities are critical for maintaining aseptic conditions and ensuring product integrity.
Applying predictive maintenance solutions to clean utilities provides several advantages, including improved utility system reliability and integrity, reduced contamination risk, and ensured compliance with regulatory requirements.
Production Line
In the pharma industry, a production line refers to the sequence of steps involved in manufacturing pharmaceutical products. Each stage requires specialized equipment and facilities to ensure product quality and compliance with regulatory standards.
This process typically includes assets such as mixing and blending equipment, granulation machines, tablet compression instruments, and coating and encapsulation machines.
Predictive maintenance (PdM) has many benefits in the pharmaceutical manufacturing process. Some of them are reducing production interruptions, optimizing resource utilization, and minimizing costs. PdM also facilitates compliance with regulatory standards while proactively identifying and addressing safety hazards.
Packaging
The final step of the manufacturing process in the pharma industry is packaging. Its importance lies in providing protection, tamper-evidence, and accurate labeling. Additionally, serialization and track-and-trace systems allow traceability and verification to combat fake drugs and comply with regulatory requirements.
Blister packaging machines, bottle filling and capping equipment, cartoning machines, labeling systems, serialization tools, and case packing machinery are some of the assets involved in this process.
Implementing predictive maintenance for pharmaceutical packaging equipment prevents packaging errors and equipment failures that could compromise product integrity and distribution readiness. It also supports timely product delivery and enhances efficiency and cost-effectiveness.
Pharma 4.0: A Broader Perspective
We use the term “Pharma 4.0” to describe the pharmaceutical industry’s evolution in the industry 4.0 ecosystem, where digital technologies, including IoT, data analytics, and AI, transform manufacturing processes.
This new paradigm improves data integration, streamlines process management, and promotes automation throughout pharmaceutical manufacturing.
At the heart of Pharma 4.0 lies predictive maintenance. It plays a crucial role in optimizing equipment reliability and performance. By harnessing predictive analytics and IoT devices, pharmaceutical companies can proactively monitor equipment health, detect potential issues before they escalate, and manage maintenance activities more efficiently.
Final words
The pharmaceutical sector is vital in improving the overall quality of life through the research, development, and production of medications and vaccines. Investing in solutions that increase the quality of the final products is imperative, and predictive maintenance is one of the best ways to achieve maintenance excellence.
PdM enhances equipment reliability and performance, minimizing downtime and production interruptions while optimizing resource utilization. This proactive approach ensures consistent product quality, regulatory compliance, and operational efficiency, aligning with the transformative framework of Pharma 4.0.
If you’d like to learn more about PdM and how it can help pharmaceutical companies improve their performance and meet regulatory standards, please contact our team.